DTH Hammer Maintanence
General Instructions
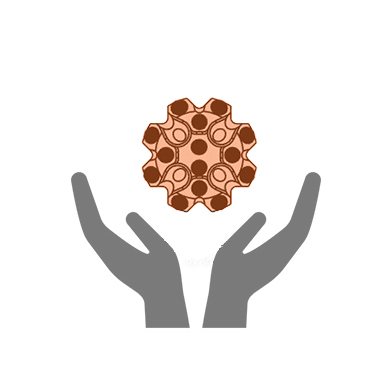
General Care
- All rods should be cleaned before use to remove scrap (sometimes found in new rods), rust scales and debris.
- Ensure that the air screen is in place and free from obstruction.
- If hammer oil is only added at each rod change, care should be taken to ensure that an adequate supply of oil is maintained to the hammer at the recommended rate. Therefore, in hard formations, it may be necessary to add oil between rod changes.
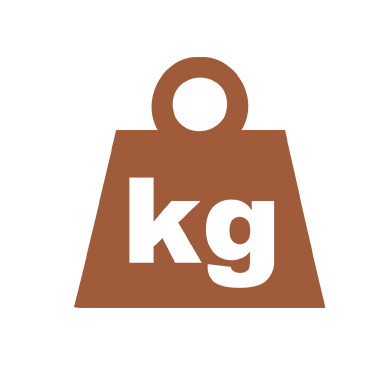
Recommended weight on the Bit
As a guide to the most efficient weight the following procedure should be used.
- Increase down-pressure until air pressure ceases to increase.
- Note hydraulic feed pressure.
- Reduce down the pressure until air pressure starts to decrease and note hydraulic feed pressure.
- Operate between these two settings.
- As a rule of thumb, rotate the bit 2 revolutions per inch (25.4mm) of penetration.
- Rotation too slow or too fast can cause premature bit failure.
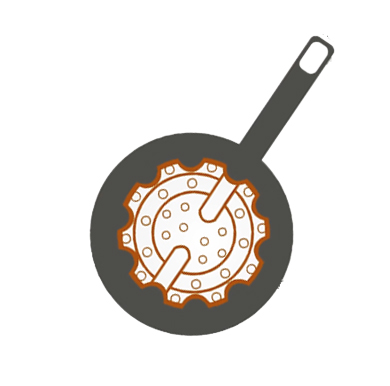
Hammer Breakout
- Pipe wrenches with flat jaws are not recommended as break-out tools. A more suitable tool would be a chain wrench, or similar type tool, which encircles the circumferences of cylinder (pipe wrenches with radial jaws approximating the curvature of the cylinder are also acceptable).
- It is not recommended to use heat on any part of the hammer to assist break-ot,as this will affect the structure of the steel.
- It is not recommended to subject the hammer to any external impact to assist break-out, as deformation of the cylinder and damage to threads may occur.
- Break-out tool placement should not be over the cylinder thread area as this can lead to distortion and ultimate breakage.
- Break-out tool placement on the bit shank is not recommended as this will damage the lower seal area. This will cause misalignment of the bit in the drive sub
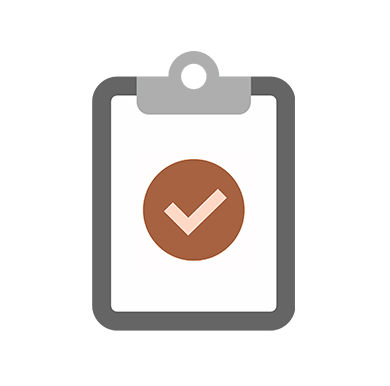
Shutdown
Before shutting down at the end of each shift, we recommend the following procedures.
- Flush hammer with air/water for few minutes and then turn off water injection.
- Flush hammer with air/oil for a few minutes. This will coat the hammer parts preventing corrosion/rust.
- Never leave the tool in a wet/muddy hole. Pull back from bottom as far as necessary to prevent the hammer sitting under water.
- It is also good practice to pour at least half litre of oil down the drill at start-up of new shift.
- If the hammer is removed from the drill rig for any reason, it is wise to pour some quantity of oil into it and block both ends. Provided the flushing, as outlined in steps one and two above have been carried out, the hammer should be stripped, cleaned and oiled before being stored.
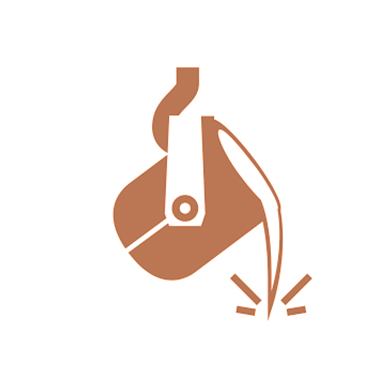
Lubrication
It is therefore extremely important that an adequate supply of the correct type of rock drill oil is constantly fed to the hammer whilst it is operating.
Failure to do so will quickly lead to excessive component wear and if the oil supply is cut off for any reason, the piston will quickly seize inside the wearsleeve, resulting in irreparable damage to both components. An airline lubrication system should be installed, preferable on the drill rig. The lubricator reservoir should be of sufficient capacity to supply the required volume of rock drill oil for a full shift. With this hammer, this might prove impractical, but the capacity should be sufficient for at least half a shift.This is equally important that the lubricator system must be adjustable and have a visual check to ensure the lubricator does not run out of oil. The amount of lubricating oil should be increased by 50% when drilling with water or foam. When new drill pipes are added to the drill string, it is recommended that a half pint (quarter of a litre) of rock drill oil is poured into the pipe to provide a good internal coating and helps prevent the hammer from running dry at any time. The grade of rock drill oil will be determined by the ambient temperature at the drilling site. If the ambient temperature is between 0 and 25 degree centigrade, then 30 grade oil should be used. If the ambient temperature is greater than 25 degree centigrade, use 50 grade oil.
DisAssembly:
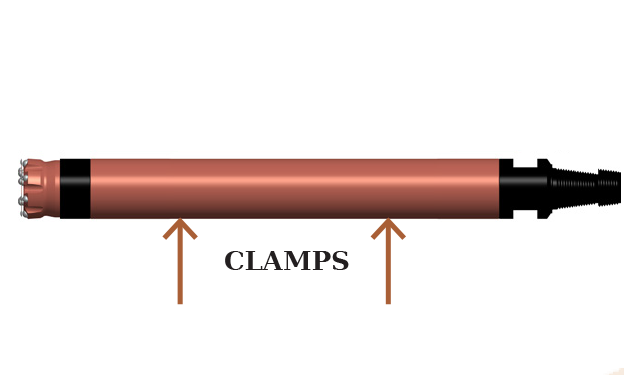


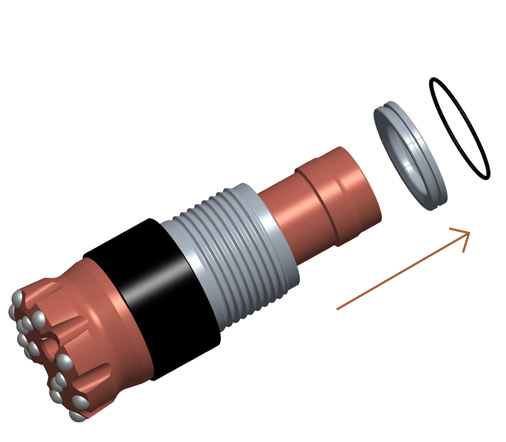
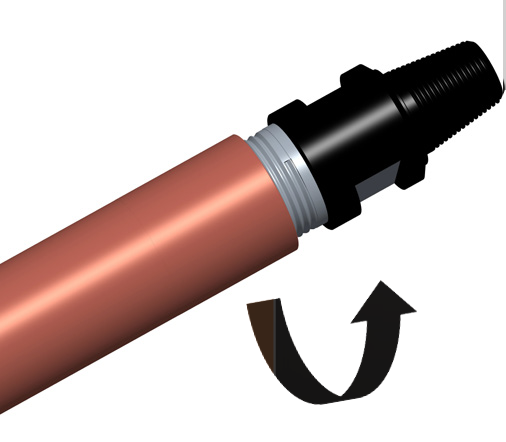
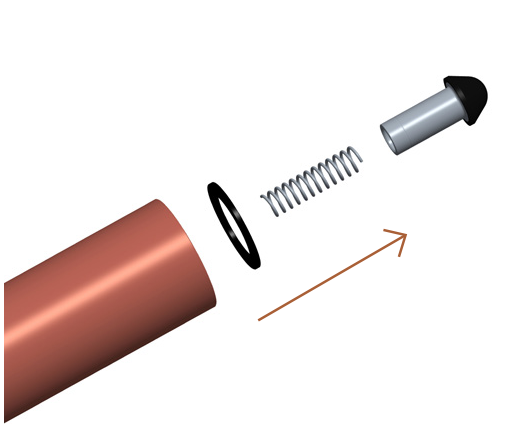
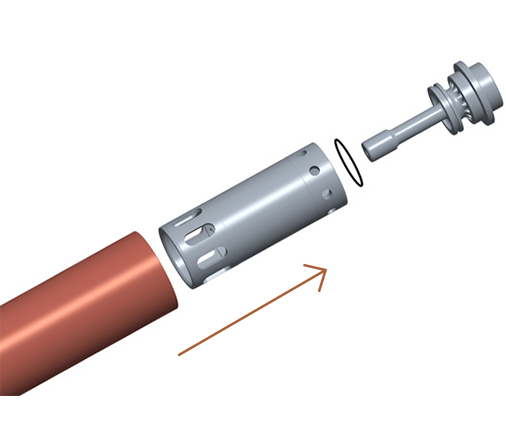
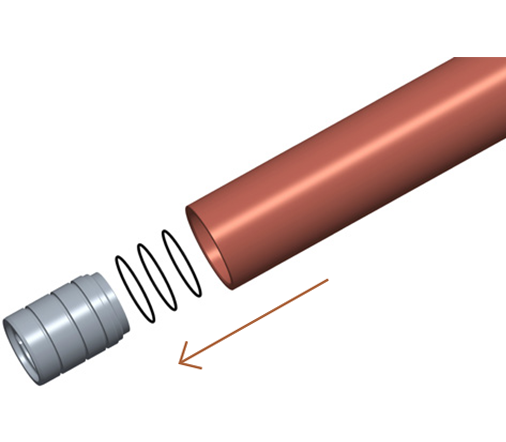
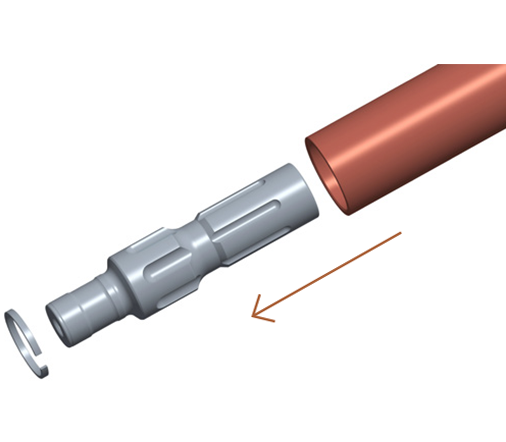
Assembly:
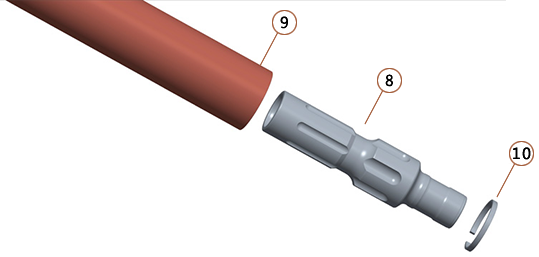
- Inspect all the components free from burrs, dirt. Liberally coat all the parts with good quality of drill oil and threads with grease.
- Place the piston (8) and piston retainer ring (10) in the wear
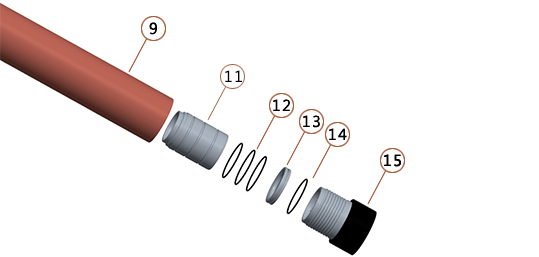
- Place the guide bush (11), along with “0” ring (12) in the wear sleeve (9).
- Place the bit retiner ring (13), along with its “0” ring (14). sleeve (9).
- Screw-up the drive sub (15) in the wear sleeve (9).
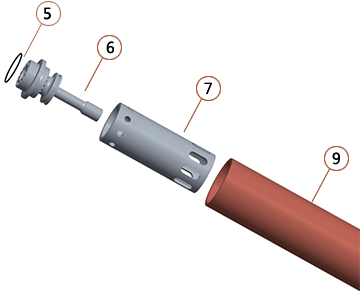
- Place the inner cylendar(7) and air distributor(6) along with the o-ring in the wear sleeve
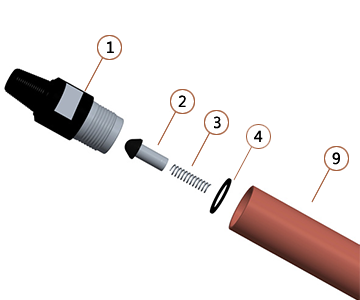
- Place the buffer ring (4), spring (3) and check valve (2) in the wear sleeve.
- Screw-up the top sub (1) and the wear sleeve (9)